- StudySolver
- /Eng302 – Task 1
Eng302 – Task 1
Semester 1, 2017
Rachael Bridges – student no. 1099071
On July 17, 1981, the United States experienced one of their worst structural failures. Two walkways, suspended from the ceiling, collapsed in the Hyatt Regency Hotel in Kansas City, Missouri. 114 people were killed and 216 injured in this preventable tragedy (Khudeira, 2011). Although the immediate cause of this incident was an upper rod and box beam failure, there were numerous project management errors that led to the construction of this unstable connection. By analysing the five processes of project management it becomes clear how these errors occurred and how the walkway collapse could have been avoided.
Initiating
The Hyatt Regency Hotel project was initiated and funded by the Crown Center Redevelopment Corporation in early 1976, with the initial scope to design and build a Hyatt Regency Hotel. In July the same year, Gillum Colaco, Structural engineers (known as GCE International, Inc., since 1983) were chosen as the consulting structural engineering firm and entered a standard contract (project charter) to complete all structural engineering services for the hotel (Texas AM University, 2009). The project manager was Daniel M. Duncan and the Engineer of Record (EOR) was Jack D. Gillum (Texas AM University, 2009). It appears that the initiation processes were completed appropriately in accordance with the steps outlined by (Project Management Institute, 2013).
Planning
During the planning stage the total scope for the engineers was established to include all structural engineering for a 35-storey, 750-room concrete guest tower with a revolving restaurant on top and a 4-storey function block with a long-spanning atrium in the middle (Luth, 2000). The objective was to build a hotel in compliance with the Kansas City building codes and to meet the needs of the stakeholders with the major stakeholder being the owner. Owner involvement is encouraged in planning stages to ensure a well-defined project scope and Crown Center was involved in developing various plans and the basic design with GCE and the architects (Luth, 2000).
A general contractor, Eldridge Construction Company, was employed and chose to use the fast track method of delivery. This method limited the time and quality control applied to the design and construction phases (Luth, 2000). According to Graph 1 from (Peebles, 2017), there should be significant effort placed into the planning of a project and this would be directly related to the amount of time spent on planning. Therefore, either the fast track method should not have been used or the project manager should have been aware of the effort required during planning and thus ensured they met this standard.
Graph 1: Planning and Control Effort Profile
Executing
The execution of the project involves completing the work outlined within the plans. One aspect of this is to co-ordinate the people and resources involved with the project such as acquiring the project team and assigning roles. Prior to completion of the project two key team members left the engineering firm so only the project manager had any history with the design and planning of the project (Luth, 2000). This would not have been an issue if the project manager had spent time developing the new team and communicating with them effectively so that they understood the project to date, the expected outcomes and their roles in achieving them.
The general contractor chose a fabricator (Havens Steel Company) for the steel works of the hotel. GCE considered the fabricator’s engineering manager as an expert in designing connections due to previous consultations on other projects. It was common practice in Kansas City at the time for engineers to leave most of the connection details to be decided by the fabricator as this allows them to tailor these details to suit their shop practice (Luth, 2000). This appears to have been a reasonable resource allocation to maintain a good working relationship between Havens Steel and GCE.
A miscommunication occurred in early January 1979, when the fabricator’s engineering manager called the project manager to discuss a change in the design plans. The request was to change the continuous rods supporting the second and fourth floor walkways and make them discontinuous and offset at the fourth floor. The project manager agreed over the phone that this change would be acceptable, however, he then asked the fabricator to submit a formal request for change which was never completed (Luth, 2000). Not long after, the fabricator removed the project from his engineering department and sent partially completed shop drawings to an outside engineering firm. The outside detailer assumed that the connection design was complete due to lack of detail on the drawings (Luth, 2000). This incident was not appropriately managed as there was no follow up by the project manager when he did not receive the formal change request and the fabricator’s engineer should have ensured the outside detailer was aware that the design was incomplete. These errors lead to the construction of a connection that had never been properly designed.
As part of the executing process, the quality requirements and quality control should be audited to ensure the project is meeting the correct standards, to enable quality assurance (Project Management Institute, 2013). GCE did perform design checks and it was noted that during a check the project manager was approached with concerns about the strength of the hanger rod. A technician had calculated that the rod did not work as A36 steel and when asked the project manager responded from memory that the rod was high-strength and he did not attempt to verify this (Luth, 2000). Verification of the rod strength should have occurred by checking the appropriate documentation and this would have led to the discovery of the connection issue. As part of the executing process it is the project manager’s responsibility to manage their team by monitoring their performances, providing feedback, resolving issues and managing changes to optimise the project performance (Project Management Institute, 2013). By not verifying the rod strength the project manager failed to provide feedback or resolve the technician’s issue and did not correct the underlying connection error.
Monitoring and controlling
The monitoring and controlling phase of the Hyatt Regency Hotel project was inadequate. These processes should include monitoring, reviewing and regulating the progress and performance of the project and observing and measuring the performance regularly and consistently (Project Management Institute, 2013). On three separate occasions the EOR was turned down by the owner when requesting site representation as the owner preferred to minimise costs (Luth, 2000). Another process of monitoring and controlling a project is to identify required changes to plans and initiate and control these changes to avoid future complications (Project Management Institute, 2013). The change of the connection detail from the design plan was never properly initiated due to the lack of submission of a formal request for change from the fabricator and it was not controlled by the project manager who did not flag this connection for further review or make any effort to follow up the request with the fabricator.
The owner had retained General Testing Laboratories to perform the full-time inspection and materials testing services while the hotel was constructed, however, they were terminated following an incident involving the atrium roof collapsing (Luth, 2000). The project was completed without a testing lab as by the owner’s authority, the EOR recommended an inspection of every connection in the atrium and the owner employed an independent engineer to do so and perform a design check. The EOR performed an in-house check of the steel and concrete connection drawings. During this check, the strength of the hanger rods was questioned again and the project manager still did not attempt to verify his claim that the rod was high-strength (Luth, 2000). No problems were discovered during the independent engineer’s or the EOR’s in-house checks (Luth, 2000). This indicates that the checks were not thorough enough and a standard checking process should be devised to include close examination of all aspects of the design plans.
Closing
Closing a project involves formally completing the project and contractual obligations, finalising and verifying all activities are complete, archiving project documents and closing out procurements. Acceptance from the client should be obtained and a post-project review should be conducted (Project Management Institute, 2013). Before the project was complete the general contractor filed for bankruptcy so it was the owner who finalised the construction and the project (Luth, 2000). There is no mention of GCE performing a post-project review. Instead an inspection company, hired by the owner, conducted a review and did not notice any deformations of the connection or walkway deflection. However, seven weeks before the opening of the Hyatt a workman noticed the walkways deflecting up to ¾ of an inch and reported this to the architect’s representative with no follow up (Gillum, 2000). Also, during the hotel’s first year of operation it was noted in a memo that the walkway handrails were deforming with no follow up and when covering the box beams with drywall a workman noticed bending in the box beam and did not mention this to anyone (Gillum, 2000). The rest of the closing processes were completed and the hotel opened in July 1980 (Luth, 2000).
Summary of Outcomes/Lessons Learnt
The Hyatt Regency Hotel would operate smoothly for approximately one year before the collapse of the second and fourth floor walkways. The cause of the collapse was due to the construction of an incomplete connection design on the fourth-floor walkway, lack of communication between the project manager and fabricator regarding the connection, poor detail in design drawings, poor review of design drawings and poor field inspections during and post-construction.
Eventually the hotel did rebuild and replaced the suspended walkways with a single crossing on the second floor supported by large pillars (Think Reliability, Accessed 2017). However, the walkway collapse contributed to several changes in engineering practice in the United States based on the lessons learnt from this disaster. These lessons show that the project management processes should include implementing a formal review process that includes every detail of all structural designs and drawings, all concept changes must be formally processed and completed, project managers should ensure that all answers to questions about potential design flaws should be verified by reference to documents and all designs completed outside the firm should be verified by a competent professional (Luth, 2000).
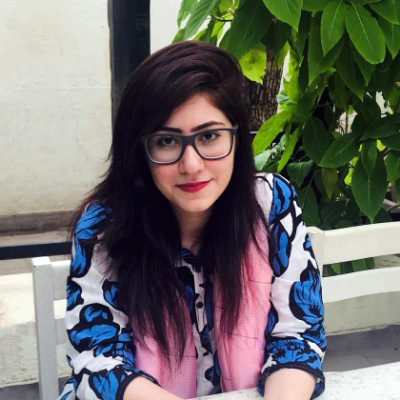
Freelance Writer
I’m a freelance writer with a bachelor’s degree in Journalism from Boston University. My work has been featured in publications like the L.A. Times, U.S. News and World Report, Farther Finance, Teen Vogue, Grammarly, The Startup, Mashable, Insider, Forbes, Writer (formerly Qordoba), MarketWatch, CNBC, and USA Today, among others.
Post a Comment
You must be logged in to post a comment.